1 Purpose of these Guidelines for Quality Assurance
The quality and sustainability of our products, our reliability and our ability to be competitive considerable contribute to to the position and importance of Franz Barta GmbH on the world market. The quality of supplies and services as well as the performance of our Suppliers have a decisive influence on the quality of our products. This is why we have the following requirements for the management system and processes of our contractual partners. These Guidelines help to avoid quality problems, to achieve smooth workflows between Franz Barta GmbH and its Suppliers, to reduce costs, to ensure environmental compatibility and sustainability of the products and processes, to reduce risks, to fulfil requests of clients and themarket as well as to act in legal conformity throughout the entire chain of Suppliers.2 Scope of application
The acknowledgment of and the compliance with these Guidelines by the Suppliers is a prerequisite for a cooperation with Franz Barta GmbH. If necessary, these Guidelines will be amended by a quality assurance agreement and they are part of the General Conditions of Purchase of Franz Barta GmbH (hereinafter referred to as “FBG”). From our partners we expect the rendering of flawless services and supplies pursuant to thecontractually agreed and determined conditions, independent from the fact whether they are rendered by them directly or by sub-suppliers. This means a 100 percent conformity of the supply obligations with respect to quality, supply fidelity and supply quantity as the basic requirement.3 Integrated Quality Management System
In order to ensure the fulfilment of high quality requirements of our clients on a long-term basis, on a consistent and sustainable basis, we require our Suppliers to introduce, maintain and develop an up-to-date and efficient quality & environmental management system (QEM). The minimumrequirement is a certification pursuant to ISO 9001 for quality management as well as ISO 14001 for environmental management. For environmental management FBG also requires its suppliers to implement a system as per ISO 50001 (due to the high energy input in production industry). For distributors this is highly recommended but not mandatory. From key Suppliers we expect the willingness to participate and actively involve themselves in the FBG Supplier development withthe aim of a certification pursuant to IATF 16949.The tasks of the Suppliers encompass the following:- Using qualified employees and ensuring their continuing training
- Intensive cooperation during the development process
- Election of qualified and reliable sub-suppliers
- Using raw materials, products and services which fulfil the requirements
- Producing in accordance with valid technical documents
- Documentation and evaluation of quality data
- Ensuring the retraceability of products
- Supply of products and services on time and without fault (zero-mistake)
- Efficient use of resources and avoidance of damaging the environment during the production and during the use
- Efficiency of the QEM-System
- continuous improvement of the processes and procedures
- improving the precautionary avoidance of mistakes (aim: zero-mistakes-supplies)
- reinforcing the reliability and processing capability in the supply chain
- insuring the compliance with the relevant legal and regulatory requirements and decrees
4 Quality targets and client specific requirements
The specific quality requirements follow from the documents on which the order is based such as framework agreements, specifications, norms and other technical documents related to the order such as certificates, drawings, samples and specimens. The Supplier has to pay regard to thetopical quality requirements submitted to him and has to ensure conformity with such quality requirements throughout his entire chain of suppliers.Chemical raw materials and carrier material are subject to a prior development- and internal release process, in the course of which new specifications and if necessary boundary samples are agreed upon with the Supplier. These are binding and part of each order.Generally valid documents, norms, provisions and legal provisions are to be complied with the Supplier and shall be obtained and up-dated by the Supplier.The Supplier employs personnel, which on the basis of adequate education, training and/or experience is qualified according to the requirements.Adequate records to determine the training and education requirements of the employees, which are responsible for quality assurance activities, are a requirement as a system element to be fulfilled by the Suppliers.Machines and equipment, the abilities of which are proven, need to be used for the production.Adequate measures for continuously supervising, determining and assessing the production process shall be complied with, with the aim of a continuous improvement.The Suppliers shall ensure the quality of their product with adequate test equipment. At each supply an acceptance certificate 3.1 in accordance with EN 10204 shall be issued to FBG.The traceability of the products shall be ensured and be proven to FBG upon request. On each package of chemical raw materials, the production date, the batch number and the expiry date shall be noted.In order to avoid qualitative impairments, damages or losses, the Supplier shall, if necessary, after consultation with FBG, determine processes and measures to ensure the correct handling, storage, packaging, delivery and transport. The execution of quality analyses is important for the continuous improvement of product- and process quality. In light of a modern quality assurance it is indispensable to record data and draw up statistics as well as to find out the process abilities. In case of deviations – in particular in case of clients’ reclamations – a cause analysis needs to be performed at once and sustainable measures to avoid such deviations and reclamations need to be defined and to be implemented.5 Testing schedules and inspection equipment
For all required tests, in particular for all entrance tests, intermediate-, end- and special tests, the Supplier shall draw up testing schedules and testing instructions. These shall in particular include the following criteria:- test criteria, sample size, testing frequency, testing procedures, inspection equipment, reaction plans in case of deviations and kind of documentation (guidance method) The testing schedules shall be implemented in a way that all possible identified mistakes from theFMEA (Failure Mode and Effects Analysis) can be detected. The Supplier ensures by setting up a continuous updating service that only the topical testing schedules and testing instructions are applied.The Supplier guarantees that all required inspection equipment for examining the products produced for the recipient are available at all times. Such inspection equipment is subject to a continuous supervision, calibration and maintenance pursuant to the requirements of the qualitymanagement system of the Supplier.The storing obligation for quality records lasts 15 years (VDA volume 1 3. edition 2008)The storing obligation starts with the drawing up of the document (see picture 1).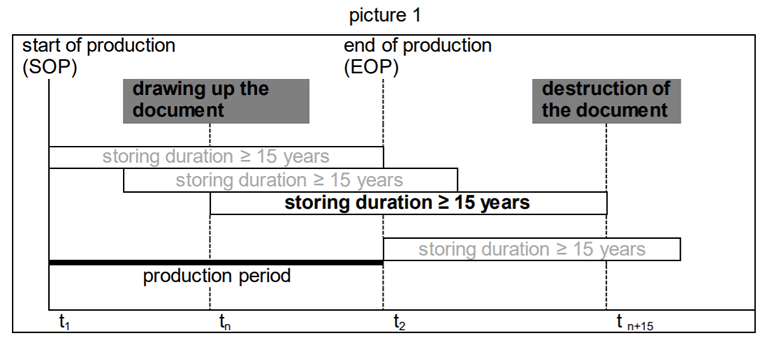
Reasoning for the storing obligation of 15 years:
- The medium vehicle life circle expanded during the last few years. It is to be assumed that only after 15 years the majority of vehicles leaves the traffic.
- The product liability act sets forth a storing obligation of at least 10 years. To this 3 more years are to be added for the claimant’s rights to raise an appeal after occurrence of the damage.
6 Entry inspection at FBG
When receiving the goods at FBG the supply is examined with regard to identity and quantity as well as clearly recognisable damages and transport damages. Deviations in these regards shall be notified to the Supplier at once.Quality deviations of the supply will be notified to the Supplier within an adequate period of at least five working days after the findings, this after they have been ascertained by FBG in the course of the ordinary course of business.7 Fault management
After determination of faulty products, the Supplier will be informed immediately and the further steps with regard to the faulty supply will be discussed (return, replacement delivery, further woks, costs).The Supplier is obliged to quickly eliminate errors and prove the effectiveness of the elimination.Applying the 8D-method is obligatory. Immediate measures shall be taken within 24 hours. FBG is to be informed immediately about the cause of error and immediate measures.If supply shortfalls occur at FBG or if the possibility exists that such supply shortfalls will occur at FBG because of quality faults or deviations with regard to the quantity or timeline, the Supplier is obliged, by using all means that are at his disposal, to immediately inform FBG and to improve the situation (extra shifts, extra tours, direct supplies, etc.).8 Product changes or discontinuation of production
In case of necessary changes of the specification of a raw material the Supplier shall inform FBG at least 6 months before implementation of such change in writing. The information on such change shall be complete so that all-encompassing examinations with regard to the effects of thequalities of the product may be performed. Furthermore, the Supplier shall provide samples, clearly marked as changed samples, with the adapted specifications, so that an examination may be performed. If the Supplier discontinues the production of a raw material without being able toprovide an adequate substitute, the Supplier is obliged to actively support FBG in the search for alternatives.The Supplier guarantees that FBG has the possibility to purchase the product in the originally specified form in the amount of the requirement for at least one year.If FGB remains silent or consents to the change, this does not relieve the Supplier from his sole responsibility for the qualities and the reliability of the raw materials.9 Supply management at FBG
In order to become part of the list of admitted suppliers at FBG, the following requirements need to be met:- sufficient systemic status (supplier self-assessment and certification status)
- positive results of the analysis of the potential
- successful audit with regard to the system on the processes upon request
- new suppliers
- deterioration of the supply quality
- in order to confirm the efficiency of a quality management system (follow-up audits)
- back classification to “B“- or “C”-supplier
- after expiration of 3 years if needed (key suppliers)
- in case of major changes in the organizational structure of a supplier
- introduction of new or changed processes
- A-supplier 100-90
- B-supplier <90-70
- C-supplier <70
10 Sustainability
FBG expects from its suppliers the introduction and continuous improvement of an environmental management system in order to assess the environmental sustainability of the processes for developing and producing products and the conformity with the requirements of the occupational health and safety provisions. This also includes the obligation to assess all options to obtain environmentally adequate and sustainable products and processes to reduce the use of resources and to implement environment-friendly packaging and logistic concepts.Supplier undertakes to collect all necessary data about current and ongoing activities in relation to CO2 footprint reduction initiatives as well as other environmental framework activities. All necessary steps are taken to implement those in its own organization and in the whole supplychain. This refers e.g. but not solely to the EU Green Deal and customer CO2 reduction initiatives such as the Daimler2039 program.Furthermore, the Supplier is obliged to perform in compliance with the high ethical and social standards of FBG and comply with the principles of the Code of Conduct of FBG.Supplier takes all necessary steps to be in compliance with requirements regarding corruption, labor law, non-discrimination and social compliance in general (stipulated in detail in e.g. ISO45001). A certification as per ISO45001 is not required but should be achieved in the long run.The contractual parties also are obliged to treat non-public business and technical details, which they get to know during the business relation, as trade secrets. Sub-suppliers are to be obliged accordingly.15.01.2022